Massives Holz-Powerrack für Dein Homegym

Diese Seite erhält eine Provision für Artikel, die über Links auf dieser Website gekauft werden, einschließlich Amazon Associates und andere Affiliate-Werbeprogramme
Beachte den Hinweis am Ende des Artikels!
Ein Powerrack aus Holz ist eine günstigere Alternative zu Metall Racks. Dies gilt umso mehr, wenn Metall-Racks ausverkauft sind. Ein DIY Holz Powerrack ist dann die einzige Möglichkeit, sich sein eigenes Home-Gym einzurichten und auszubauen.
Gegen Powerracks aus Holz werden oft Vorurteile laut. Viele denken, dass es das Gewicht einer voll beladenen Hantelstange nicht tragen oder abfangen kann.
Demgegenüber steht die Verwendung von Holz im Brücken- und Hausbau. Holz ist ein sehr stabiles Material, das viel Kraft aufnehmen und ableiten kann. Insofern habe ich keine Zweifel an der Stabilität eines Holz-Powerracks.
Es ist beim Bau eines Powerracks aus Holz wichtig, das richtige Holz zu verwenden. Ich habe Lärche gewählt, weil es eine sehr gute Druck-, Biege- und Zugfestigkeit besitzt.
Baue bessere Möbel
Mit Stammprojekte möchte ich Dir das Wissen vermitteln, mit dem Du Deine Projekte realisieren kannst.
Der Newsletter enthält anwendbare Tipps, Wissensartikel sowie aktuelle Projekte und Angebote.
Gleichzeitig sind die Maße entscheidend. Ich wollte, dass das Powerrack mit Zubehör von ATX kompatibel ist. Die Balken sind deswegen 70 mm x 70 mm stark. Eine Menge des Zubehörs für Powerracks der Serie 700 von ATX ist somit mit meinem Powerrack kompatibel.
Möchtest Du in puncto Stabilität auf Nummer sichergehen und dennoch kompatibles Zubehör haben, dann kannst Du 80 mm x 80 mm Balken verwenden. Du gewinnst so etwas mehr Stabilität und Dein Rack ist mit denen der Serie 800 kombinierbar. Möglicherweise musst Du dann aber vorher noch die Maße etwas anpassen (s. deren Webseite und Maße).
Weitere Projekte, die ich für mein Home-Gym gebaut habe:
Mit einem Hantelscheibenständer haben Deine Gewichte einen festen Platz in Deinem Homegym. Es sieht dadurch aufgeräumter und ansprechender aus, die Scheiben können nicht umfallen oder etwas beschädigen. Zusätzlich wird Dein Training entspannter, weil Du immer an die Gewichte rankommst, die Du gerade brauchst.
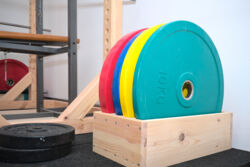
Eine Gewichtheber-Plattform ist eine großartige Ergänzung für Dein Home-Gym. Sie ist nützlich für eine Reihe von Übungen und bietet einige Vorteile für das Training. Der Kauf einer Deadlift-Platform ist sehr kostspielig. In diesem Projekt zeige ich Dir, wie Du die Plattform – mit allen Vorteilen – kostengünstig selber bauen kannst.
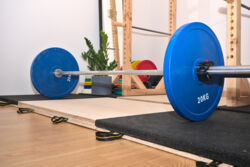
Die Teile des Powerracks
Wie bereits erwähnt, habe ich Lärchenbalken aufgrund der guten Eigenschaften benutzt.
Bei der Holzauswahl solltest Du darauf achten, dass das Holz dicht gewachsen ist. Das bedeutet, dass die Balken möglichst enge Jahresringe haben sollten.
Nummer | Beschreibung | Menge | Länge | Breite | Stärke | Material |
---|---|---|---|---|---|---|
B-Q | Querbalken | 2 | 794 mm | 70 mm | 70 mm | Lärche |
B-L | Längsbalken | 2 | 1.220 mm | 70 mm | 70 mm | Lärche |
S-Q | Querschwelle | 2 | 1.010 mm | 70 mm | 70 mm | Lärche |
S-L | Längsschwelle | 1 | 1.174 mm | 70 mm | 70 mm | Lärche |
KFB | Kopf-/Fußband | 8 | 350 mm | 70 mm | 70 mm | Lärche |
EV | Eckverbinder | 10 | 140 mm | 70 mm | 70 mm | Lärche |
PF | Pfosten | 4 | 2.000 mm | 70 mm | 70 mm | Lärche |
Alle Maße in mm |
Als Alternative zu Lärchenbalken könntest Du auch Multiplexplatten verwenden. Das Rack könnte dadurch noch stabiler werden. Für jeden Balken müsstest Du dann zwei 35 mm starke Plattenzuschnitte verleimen.
⚠️ Holz hat unterschiedliche Dichten und kann Fehlstellen enthalten. Das wirkt sich auf die Stabilität aus! Prüfe jedes Projekt auf die Korrektheit von Statik und Konstruktion!
Herstellen der Teile
Ablängen der Holzbalken
Zu Beginn habe ich die 2m langen Holzbalken abgelängt. Ich habe damit begonnen, die Kopf- und Fußbänder zuzuschneiden. Hier hat sich die Zugfunktion der CS 70 wieder einmal bewährt.

Das Ablängen der längeren Balken gestaltete sich etwas kniffliger. Ich wollte die Balken wiederholgenau ablängen, damit alle die gleiche Länge haben. Es musste also ein Anschlag mit Stopp her.
Ein Trick, lange Balken mit der Zugfunktion abzulängen, ist, den Winkelanschlag möglichst weit rechts am Sägetisch zu befestigen und den Anschlag des Parallelanschlags am Winkelanschlag zu verwenden. Auf diese Weise konnte ich sogar die beiden 1.220 mm Längsbalken ablängen. Es gibt aber einen Nachteil:
Bei dieser Methode wird der Balken im Bereich des Sägeblattes und des Schnittes nicht abgestützt. Hierdurch kann ein Kick-Back entstehen. Der Balken muss also abgestützt werden. Um den Balken zu stützen habe ich in die linke Nut eine Hebelzwinge eingesetzt und damit den Balken fixiert (leider erst, nachdem ich das Foto unten gemacht habe).

Nach den Ablängschnitten habe ich die Verbindungen an den zugeschnittenen Balken hergestellt.
Herstellen der Verbindungen
Beim Bau des Powerracks gibt es zwei Verbindungen: Erstens, die Überblattung mit der alle Balken außer den Kopf- und Fußbändern verbunden werden.
Die zweite Verbindung ist die „halbe Gehrungsverbindung“, mit denen die Bänder an die übrigen Balken angepasst werden. „Halbe Gehrungsverbindung“ deswegen, weil es im Prinzip eine winklige stumpfe Verbindung ist.
Die Gehrung an den Bändern habe ich mit dem Winkelanschlag und der Zugfunktion angeschnitten. Hätte ich das Sägeblatt auf einen 45° Winkel eingestellt, hätte die Schnitttiefe nicht gereicht.

Nach den Gehrungsschnitten habe ich die Überblattungen auf den übrigen Balken angezeichnet, um sie auf der CS 70 sauber ausarbeiten zu können.
Hierbei habe ich erst ⅓ zu ⅔ angezeichnet, die Verbindungen später aber ½ zu ½ ausgearbeitet. Bei ⅓ zu ⅔ wäre der Balken, bei dem nur ⅓ an Materialstärke stehen geblieben wäre, unnötig geschwächt worden.

Die Überblattungen habe ich wieder auf der CS 70 mit der Zugfunktion geschnitten. Ich habe den Längsanschlag verkehrt herum angebracht, um einen Anschlag für die Breite der Überblattung zu haben.

Bei den meisten Balken habe ich die Überblattung mit vielen einzelnen Zugsägeschnitten gesägt. Die beiden Querbalken (B-Q) waren „nur“ knapp 80 cm lang. Das erschien mir vertretbar, um sie senkrecht an einen erhöhten Hilfsanschlag zu zwingen und mit nur einem zweiten Sägeschnitt die Verbindung zu schneiden.

Durch den Hilfsanschlag habe ich mir ein wenig Zeit gespart, da ich mit einem Schnitt erreicht habe, was sonst eine Menge Zugschnitte erfordert hätte.

Nach dem Herstellen der Überblattungen waren die Pfosten die einzigen Teile, die noch nicht bearbeitet waren. An diesen mussten noch die Aufnahmelöcher für das Rackzubehör eingebohrt werden.
Aufnahmelöcher für Zubehör bohren
Damit das Powerrack mit dem Zubehör von ATX kompatibel ist, müssen Bohrungen mit einem Durchmesser von 21 mm angefertigt werden. ATX verwendet einen Lochabstand von 50 mm zwischen den Borhmittelpunkten.
Ich habe mich an dieses Lochraster gehalten. Du kannst den Lochabstand erhöhen, um dem Rack etwas mehr Stabilität zu geben.
Es gibt jedoch einige Zubehörteile, die genau diesen Lochabstand benötigen. Prüfe am besten, ob und wo Du diese verwenden möchtest und passe dementsprechend die Lochreihe an.

Die Aufnahmelöcher habe ich auf meinem Bohrständer mit einem 21 mm Schlangenborher gebohrt. Ich habe jeweils zwei Balken aufeinander gezwingt und dann erst die Löcher gebohrt. Auf diese Weise fluchten die Löcher später exakt.
Mein Bohrer war zu kurz, um in einem Arbeitsschritt durch beide Balken zu bohren. Im unteren Balken kam ich jeweils nur bis zur Hälfte. Das war aber vollkommen ausreichend für den Arbeitsflow.
Nachdem es aber besser und vor allem schneller ist, gleich zwei Balken in einem Rutsch fertig zu machen, habe ich Dir einen längeren Schlangenbohrer verlinkt.
Nachdem ich im ersten Balken alle Löcher gebohrt hatte, habe ich den unteren „angebohrten“ Balken auf einen unbearbeiteten Balken gezwingt. Der Balken hat mir quasi als „Bohrschablone“ gedient.
Die Aufnahmelöcher habe ich auf meinem Bohrständer gebohrt. Ich habe jeweils zwei Balken aufeinander gezwingt und dann erst die Löcher gebohrt. Auf diese Weise fluchten die Löcher später exakt.
Mein Bohrer war zu kurz, um in einem Arbeitsschritt durch beide Balken zu bohren. Im unteren Balken kam ich jeweils nur bis zur Hälfte. Das war aber vollkommen ausreichend für den Arbeitsflow.
Nachdem ich im ersten Balken alle Löcher gebohrt hatte, habe ich den unteren „angebohrten“ Balken auf einen unbearbeiteten Balken gezwingt. Der Balken hat mir quasi als „Bohrschablone“ gedient.
Sobald die vier Balken ihre Aufnahmelöcher hatten, musste ich sie noch fertig bearbeiten. Dazu habe ich mit meiner Perles Oberfräse und einem Abrundfräser die Kanten der Löcher gebrochen.
Das schützt die Kanten davor, dass sie bei der Benutzung ausbrechen. Gleichzeitig wird das Einführen von Zubehör in die Löcher erleichtert.
Das Rack ist nach der Bearbeitung der Löcher fertig zum Zusammenbau. Das Powerrack braucht aber noch eine Unterlage. Deswegen habe ich erst noch eine Plattform gebaut.
Baue bessere Möbel
Mit Stammprojekte möchte ich Dir das Wissen vermitteln, mit dem Du Deine Projekte realisieren kannst.
Der Newsletter enthält anwendbare Tipps, Wissensartikel sowie aktuelle Projekte und Angebote.
Powerrack Plattform bauen
Der Zweck der Plattform liegt darin, den Boden vor herunterfallenden Hantelscheiben zu schützen. Gleichzeitig soll beim Absetzen von Gewichten die Lautstärke etwas reduziert werden.
Die Plattform ist wie die Deadlift Platform für mein Homegym aufgebaut:
- Die unterste Schicht ist eine 15 mm OSB/3 Platte.
- Links und rechts des Racks wird darauf eine 30 mm Gummi Fallschutz-/Bodenschutzmatte gelegt.
- In der Mitte – dem Standbereich des Powerracks – wird eine zweite 15 mm OSB/3 Platte zur Aufdopplung und darauf eine 15 mm Multiplexplatte gelegt.
Die Teile der Powerrack Plattform
Nummer | Beschreibung | Menge | Länge | Breite | Stärke | Material |
---|---|---|---|---|---|---|
GP | OSB/3 Grundplatte | 1 | 2.500 mm | 1.000 mm | 15 mm | OSB/3 |
GP-AD | Aufdopplung Grundplatte | 1 | 1.000 mm | 1.000 mm | 15 mm | OSB/3 |
DP-SF | Deckplatte Standfläche | 1 | 1.000 mm | 1.000 mm | 15 mm | Birke MPX |
FSM | Fallschutzmatte | 2 | 750 mm | 1.000 mm | 30 mm | Gummi |
Alle Maße in mm |
Für die Grundplatte habe ich 2.050 mm x 625mm OSB/3 Platten mit Nut und Feder verwendet, da ich eine zusammenhängende OSB/3 Platte nicht transportieren konnte. Die Platten habe ich an der Nut und Feder Verbindung verleimt.

Bevor ich die einzelnen Segmente der Grundplatte an der Nut und Feder Verbindung verleimen konnte, musste ich sie zuerst zuschneiden. Dazu habe ich die Platten für die Grundplatten auf 1.000 mm abgelängt.
Vier 1.000 mm x 625 mm Platten ergeben die 2.500 mm x 1.000 mm Grundplatte. Für die Aufdopplung habe ich ebenfalls zwei Zuschnitte verwendet. Die Multiplex Deckplatte habe ich mir im Baumarkt bereits final zuschneiden lassen.

Als nächstes habe ich mir die Gummiplatte zugeschnitten. Ich habe meine Makita Tauchsäge dazu benutzt.
Wenn Du das ebenfalls machst, dann verwende in jedem Fall ein Sägeblatt für Längsschnitte. Alles andere belastet die Kreissäge unnötig, da der Gummi sehr dicht ist.
Alternativ kannst Du eine Stichsäge oder ein Teppich-/Cuttermesser mit einem Anschlag benutzen.

Oben siehst Du den Aufbau der Plattform: Die OSB/3 Grundplatte, die Aufdopplung mit einer weiteren OSB/3 Platte für die Standfläche, auf der Aufdopplung die MPX Platte für die Standfläche sowie die beiden Gummimatten.
Für das Bild habe ich absichtlich eine etwas schmalere Multiplexplatte auf die Aufdopplung gelegt, damit Du diese sehen kannst.
Die Aufdopplung habe ich mit der untenliegenden Grundplatte verschraubt. Die Multiplexplatte habe ich mit doppelseitigem Klebeband auf die Aufdopplung geklebt.
Verschrauben wollte ich sie aus optischen Gründen nicht. Verleimen wollte ich die Platten nicht, falls ich die Plattform jemals wieder abbauen sollte. So kann ich die teurere MPX Platte noch für andere Dinge verwenden. Die Gummimatten sind einfach nur aufgelegt – sie halten von alleine. Unter der Plattform habe ich eine Antirutschmatte ausgelegt, um das Parkett vor Kratzern zu schützen.
Aufbau des Powerracks
Der Aufbau des Powerracks gestaltet sich durch die Überblattungen recht einfach. Als Erstes habe ich die beiden linken und rechten Rahmen verschraubt. Ich habe dazu zwei Pfosten mit je einem Querbalken und Querschwelle verschraubt.

Ich habe in jeder Ecke ein Kopf-/Fußband eingesetzt und verschraubt, um die Rahmen auszusteifen. Die Löcher sollten vor dem Verschrauben vorgebohrt werden, damit das Holz nicht splittert.

Bevor ich die Rahmen aufgestellt habe, habe ich an einem Rahmen den vorderen Längsbalken und am anderen Rahmen den hinteren Längsbalken verschraubt. Die Rahmen haben sich dadurch nach dem Aufstellen gegenseitig gestützt, weil sie direkt lose verbunden waren. So konnte ich sie bequem miteinander verbinden.

Nach dem Aufstellen habe ich in den übrigen Ecken noch weitere Eckverbinder verschraubt. Sie dienen dazu, das Rack zusätzlich zu stabilisieren und auszusteifen. So hat das Powerrack kaum Spiel, obwohl es nicht mit dem Boden verschraubt ist.

Das fertige Powerrack steht für sich schon recht stabil. Liegt eine beladene Hantelstange auf den Ablagen, dann bewegt sich nahezu nichts mehr.
Verpasse keine Projekte
Melde Dich für den Newsletter an und erhalte alle neuen Projekte, Wissensartikel und Jigs direkt als erster.

Für das Powerrack habe ich mir bisher eine Ablage für die Hantelstange sowie eine Halterung für die Hantelstange gebaut.
Vor der Trainingsfläche des Powerracks liegt meine Deadlift Platform, die ich mir für das Kreuzheben gebaut habe. Links und rechts nebem dem Rack habe ich meine ATX Hantelscheiben in einen Hantelscheibenständer einsortiert.
Für die Notablagen habe ich 20 mm starken Rundstahl verwendet. Ich empfehle Dir, ebenfalls Rundstahl zu nutzen. In anderen Anleitungen werden oft Rundrohre/Pipes benutzt. Diese halten deutlich weniger aus, als massiver Stahl.
Die ATX Pin Pipes Safeties bestehen ebenfalls aus Rundstahl und haben eine Belastbarkeit von 1.000kg/Paar. Meine Notablagen werden daher sicher ihrem Zweck gerecht werden – selbst wenn sie nur die Hälfte aushalten.

Ich habe in meinem Powerrack schon mehrfach trainiert. Es macht riesigen Spaß, damit zu trainieren und ich habe großes Vertrauen in die Stabilität des Powerracks. Es ist sehr massiv geworden.
Hast Du Fragen oder Anmerkungen zum Powerrack oder seiner Stabilität? Schreib mir einen Kommentar!
⚠️ Holz hat unterschiedliche Dichten und kann Fehlstellen enthalten. Das wirkt sich auf die Stabilität aus! Prüfe jedes Projekt auf die Korrektheit von Statik und Konstruktion!
Dieser Artikel dient der Unterhaltung und Information. Er ist keine Bauanleitung. Sollte der Bau eines Powerrack anhand der hier vermittelten Informationen erfolgen, geschieht dies auf eigene Gefahr. Fehlende Kenntnisse bei Holzbearbeitung, Statik und Konstruktionsmethoden können lebensgefährliche Verletzungen bis hin zum Tod hervorrufen.
Kommentare
Hallo,
Habe über google dein Projekt Powerrack gefunden :-)
Ich bin dabei mir auch ein Power-Rack zu planen allerdings weiß ich noch nicht ob auch Stahl 4KT Rohr 50x50x3 oder aus Holz.
Die Frage ist, ist das Holz auch stabil ohne das etwas wackelt ?
Bankdrücken 160kg
Kniebeuge 200kg
Mittig soll noch ein Latzug verbaut werden
Dachte evtl an 4KT 80mm Holz um Zubehör von der ATX800 Reihe zu verwenden ?
Danke und ein schönes Wochenende
Alex
Hallo Alex,
mein Rack hat lateral (seitlich) ein wenig Spiel, aber nicht so, dass es mich beunruhigen würde. Die Stabilität hängt natürlich davon ab, wie genau Du arbeitest. Mit Winkelverbindern wie diesen hier kannst Du zusätzliche Stabilität reinbringen.
Grüße
Moin.
Sehr, Sehr interessant. Das sieht ja super aus! Da habe ich direkt mal paar Fragen.
Leider habe ich nur eine Deckenhöhe von 1,99m (Müsste dann vielleicht eins bauen was nur 1,95-1,97 hoch ist) WENN ich das Rack nachbaue, wäre es trotzdem noch kompatibel mit ein Latzug ?
Wie viel KG hält das ganze aus?
Hält das Rack aus Holz quasi genauso lange wie eins aus Stahl?
Vielen Dank und gute Arbeit!
Hallo Danny,
ob ein Latzug noch kompatibel ist, müsstest Du anhand den Spezifikationen bei ATX nachschauen. Ich glaube fast, dass die Deckenhöhe zu niedrig ist. Andererseits gibt es auch Anleitungen für Latzugeigenbauten (Googlen).
Grüße
Hallo Tobias,
genau so eine Anleitung habe ich gesucht. Ich möchte mir auch das Rack nachbauen. Allerdings soll meines in den Garten. Hast du hierzu einen Tipp zum Holz und welche Imprägnierung oder Lack du empfehlen kannst. Mir ist klar, dass es draußen nicht für die Ewigkeit halten wird, aber im Haus ist leider kein Platz.
Vielen Dank für deine Hilfe.
Hallo Martin,
es freut mich sehr, dass Dir der Artikel gefallen hat! Ein Rack im Garten ist ein geiles Projekt, trotzdem wäre ich hier sehr vorsichtig. Du solltest Dir eingehend Gedanken über den Holzschutz machen.
Das fängt beim konstruktiven Holzschutz an. Dieser besteht mindestens aus einem trockenen Untergrund, d.h. eine Drainage (Untergrund aus Sand oder Splitt auf der Wasserdurchlässige Gummimatten liegen) muss her. Bestenfalls ist das Ganze natürlich überdacht. Das muss grundsätzlich nichts besonderes sein. Eine Platte als Schrägdach ist schonmal besser als nichts – aber eben so einer dimensioniert, dass bestenfalls nichts nass wird.
Als nächstes ist die Holzauswahl wichtig. Die Dauerhaftigkeitsklassen für Holz geben Dir da eine Orientierungshilfe. Am besten wäre Klasse I oder II, aber da bist du preislich weit über einem Rack aus Metall. Bleibt also Klasse III mit sibirischer Lärche, europäischer Lärche und europäischer Douglasie (in dieser Reihenfolge). Wenn Du zufällig an gute Eichenbohlen rankommst, wäre das aufgrund des hohen Gerbsäuregehalts ebenfalls eine gute Wahl.
Für den Holzschutz habe ich leider keine Empfehlung für Dich, weil ich etwas vergleichbares noch nicht umgesetzt habe. Ich würde aber vermutlich das Rack mit einer Holzschutzimprägnierung grundieren und danach mit einer Wetterschutzfarbe/-lackierung streichen. Du kannst Dir auch überlegen, ob Bootslack eine Alternative ist.
Da Du aber an/mit dem Rack trainierst, wird der Holzschutz unweigerlich leiden und durchlässig werden. Das solltest Du bei Deiner Planung ebenfalls berücksichtigen. Wenn das immer wieder aufgefrischt werden muss, geht das auch ins Geld (und ein Metallrack kann sich ggf. doch rechnen).
Durch die Wettereinwirkung wird das Holz auch arbeiten. Das kann sich auf die Verbindungen auswirken. Die sind entsprechend stabil zu fertigen. Außerdem können sich Rissen bilden. Da wird nicht so einfach zu beurteilen sein, ob die nur oberflächlich sind oder doch die Stabilität beeinträchtigen. Wenn Du jetzt schon weißt, dass Du dem Rack dann nicht mehr vertraust, würde ich das Projekt überdenken.
Insgesamt: Coole Idee. Ist das Rack überdacht, dann go for it! Ist es dem Wetter ausgesetzt, wird das Projekt sehr anspruchsvoll und ein Metallrack ist vielleicht doch die bessere Alternative.
PS Ich plane, die Pläne für das Rack zu veröffentlichen. Wenn Du daran Interesse hast, dann melde Dich doch für den Newsletter an. Die Info, wie Du an die Pläne kommst schicke ich Dir dann per Mail zu, wenn es so weit ist.
Beste Grüße
Grüße, tolle Idee mit dem Powerrack, würde ich gerne nachbauen. Gibt es da vielleicht einen genaueren Plan? Vielen Dank
Erstmal klasse Projekt.
Wie viel hast du für den ganzen Spaß ausgegeben, um eine grobe Richtung zu haben, wie viel ich einplanen muss ?
Hallo Anton,
das Holz für das Rack dürfte mich damals etwa 150-200 € gekostet haben. Die OSB Platten kosten nur wenige Euro. Die Bodenschutzmatten waren mit um die 150 € ebenfalls recht teuer. Ansonsten kommt halt noch Verbrauchsmaterial dazu (Schrauben, etc.).
Zusätzlich habe ich einen 21 mm Bohrer gekauft.
Das Hauptproblem, das ich sehe, ist, dass die Holzpreise enorm angezogen haben und ich nicht glaube, dass meine Kosten noch einen Vergleich darstellen können.
Beste Grüße
Hey, mega geiles Projekt!! Ich bin auch gerade ein Power Rack am bauen, nur fehlt mir eine idee wie ich die Hantelablage bauen kann. Bei dir ist das leider nicht erklärt, hast du da evtl genauere Angaben zu? ich habe 20er Löcher gebohrt.
Hi Tobias,
echt ein klasse Projekt und eine saubere Beschreibung.
Ich würde mir das ganze gerne nachbauen, aber leider scheitere ich am Bohrer.
Die Bohrer mit 21mm sind entweder Forstnerbohrer die zu kurz sind, so das ich nicht durch komme, oder Schlangenboher die zu lange sind um sie in meinen Bohrständer einzuspannen :(. Dein Bohrer sieht aus als könnte der bei meinem Bohrständer passen. Würdest du verraten wo du den genau her hast? ....Den Amazon-Link weiter oben habe ich ohne Erfolg versucht.
Viele Grüße
Dani
Hallo Dani,
auf Feinewerkzeuge gibt es einen 21mm Schlangenbohrer.
Beste Grüße
Hi Tobias
ich wollte mich auch mal fuer die super Anregung und die klasse Beschreibung bedanken.
dein Projekt hat mich dazu veranlasst ebenfalls ein Rack zu bauen und ich habe mich dabei an deinem Orientiert nur habe ich es aus Stahl gebaut,
Also Vielen Dank und einen schönen Tag
Hallo Wilhelm,
vielen Dank für dein Feedback. Freut mich, dass Dir mein Rack gefällt. Ich hoffe, Dir ist Dein Eigenbau gelungen und Du bist mit Deinem Rack zufrieden.
Beste Grüße
Hi Tobias,
das ist ein schönes Powerrack geworden! Da ich zwar schon lange mit einem ATX-Rack der 500er/600er/700er Reihe liebäugele, aber die Preise und Lieferzeiten immer mehr ansteigen, ist der Eigenbau eine gute Alternative. Ich würde mich freuen, wenn Du mir folgende Fragen beantworten könntest (sie sind wahrscheinlich auch für künftige Bastler interessant):
noch ausreichend?
Eine Übungsplattform habe ich mir bereits selbst gebaut (2.5 m x 2.5 m), und ich würde das
Rack gerne zur Seite schieben können, damit die ganze Fläche nutzbar ist (evtl. Holzplatte
unterlegen). Wenn man die Langhantel mit Gewicht auf die Hantelablagen legt, sollte es
auch schwer genug sein um ein Umkippen und Verschieben des Racks bei Verwendung
eines Schlingentrainres zu verhindern.
Gummibänder drüberzulegen) oder läuft man Gefahr, dass es ausbricht?
Tiefe anzubringen?
Schön wäre es noch, wenn man vorne eine Multigrip Bar aus Metall anbauen würde oder
einfach eine Metallstange (evtl. mit Öse für Schlingentrainer) für Klimmzüge. Außerdem kann
man sich auch noch Dipstangen selbst bauen und quer auf die Sicherheitsablage legen,
einfach mal googeln.
Beste Grüße
Hallo Michael,
Ich weniger Löcher bohren. Viele Löcher=Flexibilität, aber auch weniger Stabilität.
Wenn Du ausmisst, wo Deine Löcher sein müssen (Bankdrücken, Kniebeuge und was Du sonst noch brauchst) und daran orientiert zusätzliche Löcher bohrst, brauchst Du nicht so viele Löcher.
Das ist dann noch stabiler und weniger Arbeit.
Das ist immer ein Kompromiss. Sicherlich ist schmaler/kürzer/weniger tief ausreichend, es wird halt weniger komfortabel.
Kann ich Dir so nicht sagen, weil es schwer zu wiegen ist ;) Du kannst es Dir über die Dichte des Lärchenholzes ausrechnen. Je nach Dichte dürfte es um die 40-70kg haben.
Verschiebbar ist es jedenfalls.
Einen Schlingentrainer sollte halten, wenn er richtig befestigt wird, da das Rack genug Auflageläche am Bode hat. Ich würde ihn trotzdem nur anbringen, wenn Das Rack kippsicher am Boden befestigt wäre.
Nein.
Ich denke nicht, dass etwas ausbricht, wenn die Band Pegs mittig angebracht werden. Am Ende wirkt dieselbe Kraft, wie bei Gewichten. Wenn das Rack das Gewicht aushält, hält es die Band Pegs. Ausnahme sind dynamische Übungen, aber die machst Du vermutlich nicht mit >100kg Widerstand (plus Gewicht).
Dasselbe gilt für eine Klimmzugstange.
Es ist letztendlich immer eine Frage der Konstruktion und wie viel Material das Gewicht wie tragen kann. Das musst am Ende Du beurteilen.
Es ist sehr schwer hier absolute Empfehlungen zu geben.
Ja. Zwei Muliplexplatten verleimt, 20 mm Loch rein, Gewinde in die 20 mm Stahlrundstange geschnitten und mit einer Konterschraube verschraubt. Ein Artikel dazu steht noch auf der To-Do.
Hallo, gibt es zu dem Powerrack auch genauere Pläne für die Herstellung/Aufbau?
Hallo,
War es gut, 21mm Löcher zu bohren um das ATX-Zubehör zu verwenden oder würdest du eher einen 20mm bzw 20.5mm verwenden?
Danke!
Hallo Chris,
für mich waren die 21mm Löcher gut. Bei 20 mm Löchern kann ich mir vorstellen, dass sie tatsächlich zu eng sind. Da Metallbau eine deutlich höhere Fertigungstoleranz hat, kann ich mir vorstellen, dass 20,5 mm hier und da ebenfalls Probleme machen können. Mangels 20,5 mm Bohrer fehlt mir aber die Expertise.
Hat schonmal jemand die Belastbarkeit getestet. Habe vor das Rack analog der Anleitung zu bauen (selbe Maße/Materialien). Sind 250 kg Belastung machbar?
@Jonas:
Laut Wikipedia hat Lärche ein Druckfestigkeit in Faserrichtung von 55N/mm² oder 5,61kg/mm². Wenn ich mich nicht verrechnet habe, macht das bei 7x7cm 27,489kg pro Pfosten, wenn das Gewicht Senkrecht von oben wirkt. Eine Langhantel liegt auf mindestens zwei Pfosten auf. Deine 250kg wären nur auf der Basis 0,4% der theoretischen Belastbarkeit.
Ja, das Gewicht wirkt nicht senkrecht von oben, es wirken auch Zug und Biegekräfte, etc etc etc.
Der Schwachpunkt dürfte ehr die Hantelablage sein.
Ich denke nicht, das Hobbysportler in der Lage wären die Belastbarkeitgrenzen dieses Powerracks herauszufordern.
Zumal ich davon ausgehe, das Tobias an seinem Leben hängt und ehr auf Nummer sicher gegangen ist ;)
Disclaimer: Ich bin kein Statiker/Tischler/... Das oben geschrieben ist meine subjektive Meinung.
Hallo Tobias,
interessantes Projekt.
Sag' mal bitte: WIe hast du denn die Ablageklötze für die Langhantel gebaut und haben die eine Art "Schnellfeststellung"?
Viele Grüße
~Arno